A new light-sensitive polymer resin gives researchers more control over 3D-printed objects.
Since its inception in the early 1980s, 3D printing technology has emerged as a futuristic and revolutionary means of manufacturing. Among the many innovations is a technique called volumetric additive printing, in which an entire 3D object is is solidified from a photosensitive liquid material by irradiating it with different patterns of light.
This technique is highly innovative because it overcomes many of the drawbacks of layer‐by-layer fabrication of conventional 3D printers, such as long build times and rough surfaces. The types of materials available are also broader, having fewer constraints on viscosity and reactivity compared to layer printing.
In an article recently published in Advanced Materials, a team of researchers led by Maxim Shusteff of Lawrence Livermore National Laboratory reported a highly tunable strategy using a new thiol-ene photoresin.
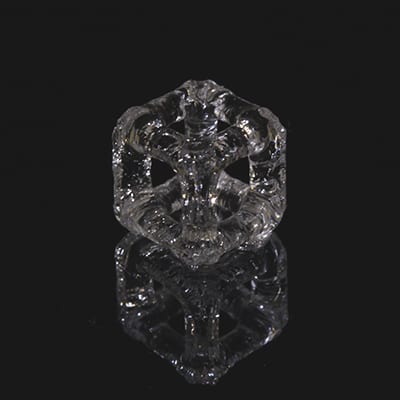
Thiol-enes are polymers formed through the polymerization between a thiol and an alkene to form a thioether. They have drawn significant attention in recent years owing to the high degree of control and tunability that researchers can exert over the reaction (something that is not always easy to do in a polymerization), and yield polymers with excellent mechanical properties.
“We made an important step toward showing the material versatility of [volumetric additive manufacturing] by adapting thiol-ene resin to this new paradigm,” said Shusteff. “Thiol-ene materials are attractive because they have well-ordered polymer networks, allowing for a much wider variety of mechanical performance from stiff and strong to soft and stretchy.”
In their study, the team applied thiol-enes to create a new class of resins. Using a 3D distribution of light, they were able to cast images generated using an algorithm onto the resin, triggering polymerization at specific locations to build 3D objects, like rings.
“It wasn’t obvious that thiol-ene cross-linking chemistry would work, because it doesn’t have the threshold response that’s needed i.e., thiol-ene isn’t inhibited by oxygen,” continued Shusteff. “We overcame this by including a chemical inhibitor.”
The approach is exciting because it can be used to make complete parts all at once without layering within a matter of seconds, says Shusteff. The team was also able to print directly onto pre-existing structures, a technique known as overprinting.
An important feature of the thiol-ene resin is the fact that it follows a “a nonlinear response to the curing illumination”, meaning the material has an energy threshold that allows the polymerization reaction that forms the hardened polymer to be highly controlled. “We showed a quantitative ability to design the resin’s response to absorbed optical energy by measuring the gelation threshold and incorporating it during our build,” said Shusteff.
Regions that are not irradiated with the right amount of energy will remain liquid and can be poured away afterward.
The team has plans to use these thiol‐ene materials as functional biological scaffolds, as the unreacted thiols can be used for surface functionalization.
“We believe that with the right commercialization partner, a printer-based on this technology can be brought to market in about 3 years,” Shusteff said. The team sees there technology finding useful application in medical and dental markets “because patient-specific geometries are important there”, as well as in creating artificial tissues and organ models from soft hydrogels.
“As with any new research area, the challenges are many,” added Shusteff. “We are working to thoroughly understand the resolution limits of this process and to improve its accuracy, which is dependent both on the optics and the photo-chemistry.”
Though continued improvements of the algorithm-defined energy estimates and experimental exposures to further enhance the technique’s capabilities, the team is optimistic that expanding material options for 3D printing technologies will pave the way for better control and complexity in 3D-printed materials.
Reference: Caitlyn C. Cook, et al., Additive Manufacturing: Highly Tunable Thiol‐Ene Photoresins for Volumetric Additive Manufacturing, Advanced Materials (2020). DOI: 10.1002/adma.202003376
This article was amended on December 7, 2020 to include quotes from Professor Shusteff