Mg-based microresonators for wirelessly powered biodegradable medical implants.
Tremendous strides have been made over the past few decades in electronics, micro-, nano-, and wireless technology, which have greatly enhanced the quality of healthcare.
Implantable medical devices, such as pacemakers, implantable cardiac defibrillators, coronary stents, hip implants, interocular lenses, and implantable insulin pumps (to name a few), are widely used to address a number of conditions, providing lasting, lifesaving treatments.
Biodegradable implants have been gaining more and more attention in recent years as they have the added benefit of removing the need for a secondary surgery for their retrieval, improving patient safety and overall comfort. A key challenge within this field of research has been in developing biodegradable power sources and manufacturing processes compatible with water-soluble devices.
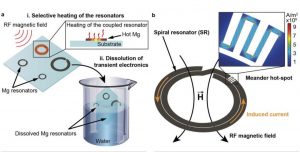
Design and fabrication of biodegradable Mg microresonators. a) Concept of using frequency‐selective, biodegradable microresonators as power receivers and microheaters for transient electronics. b) Design and FEM simulation of a spiral resonator (SR) with a meander hot spot to increase the induced current density by one to two orders of magnitude.
A group of researchers from Ecole Polytechnique Fédérale de Lausanne (EPFL) have proposed an alternative to these approaches by wirelessly powering biodegradable implanted devices using a radio-frequency magnetic field, which would reduce the amount of material implanted in the body by integrating the power supply and wireless control of the implant into one system.
“Our research aims at developing innovative microfabrication processes with minimal exposure to aqueous media to fabricate magnesium-based, water-soluble electronic components,” says Matthieu Rüegg, Ph.D. student at EPFL and co-author of the study. “The goal is to fabricate small power receivers and microheaters that can be integrated on biodegradable medical implants and thus empower personalized and minimally invasive medicine.”
Resonant circuits would lend an additional degree of control, as multiple resonators within the same implant that respond to distinct applied frequencies could be used to selectively control various functions, such drug delivery.
In their publication, the team demonstrated the design and fabrication of a magnesium(Mg)-based microresonators using an innovative dry microfabrication process in which Mg is first deposited by thermal evaporation and then patterned using photolithography and ion beam etching.
“The main challenge was to find a way to fabricate Mg microresonators with a spiral shape and a resolution of a few micrometers,” adds Rüegg. “[This] would be difficult to achieve by stencil lithography and having such a geometry is what enables us to have small resonators, which still work in a frequency range around 2 GHz.”
The resonance frequency of the Mg microresonators can be tuned to specific values by varying their geometrical parameters, which can be predicted beforehand using Fine Element Method (FEM) simulations. Their electrical performance and degradation in aqueous media highlight the wirelessly powered, frequency-selective microstructures’ promise as power receivers and microheaters for biodegradable implantable medical devices.
“The ability to selectively power and heat microresonators made of biodegradable materials is a significant step towards the use of such devices as heating and triggering elements in implantable biodegradable devices, in particular for controlled drug release and thermal therapy,” says Rüegg.
While an important step forward, work still needs to be done to integrate the resonators into workable devices and demonstrate their capabilities both in vitro and in vivo.